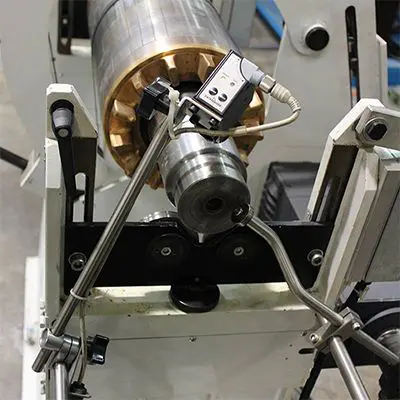
7 Simple Ways to Minimize Spindle Repair
Spindle repair services are critical to minimizing downtime and excessive repair costs. Replacing spindles, particularly custom-built tooling, can be costly for your manufacturing facility. Explore seven key processes you can implement with the help of Superior Spindle to maximize the lifetime and efficiency of your spindles and industrial machines.
1. Routinely Test Spindle Pull Force
Measure the force of your spindles at least once every six months. A drawbar pull force test is an easy step for your team to perform, or you can work with a qualified spindle repair team to receive this test. This test helps prevent vibrations and runout due to a drop in force, both of which can cause serious damage to your equipment.
Two tests every year is a great start for your spindles, but it’s important to use this test after a crash. A ground and calibrated spindle test bar can cause a crash, which may affect the force and calibration of your spindle.
2. Use Quality Lubrication
Review the type of lubrication used in your spindle maintenance procedure. Here are a few reasons that even a well-lubricated spindle may experience additional wear:
- Contaminated lubrication
- Improper fluid levels
- Incorrect lubrication as recommended by the manufacturer
- Dirty or damaged air-intake filter on an air/oil spindle assembly
Review your lubrication procedure to see if you’re using incorrect or insufficient lubrication or any spindle in your facility. Some manufacturers may recommend different lubrication features for similar spindles.
3. Maintain Lubrication
A more obvious step to keeping your spindles operating efficiently is to continue to lubricate them. Don’t attempt to lubricate a closed-unit spindle, as these are sealed and lubricated for the lifetime of the tooling. Whether you’re using an oil bath, air/oil system or another lubrication process, review the timing of lubrication application to avoid unnecessary wear.
4. Monitor Vibration Levels
Excess vibration is a primary factor in both tool wear and manufacturing efficiency. Use an external vibration test or watch the internal vibration readings to see if your machine is operating with too much vibration. This may be due to a bent spindle, worn bearings or other maintenance issues.
Don’t ignore any vibration alarms. If your machine has internal vibration sensors that are faulty, be sure to replace and calibrate them. This system is a helpful warning system to prevent excess use of worn-out spindle bearings.
5. Always Use Machine Covers
It’s common for maintenance and operation teams to remove covers to inspect the internal components of your CNC machine, turning machine or other industrial manufacturing equipment. Unfortunately, protective covers can be left off for a significant period of time. Be sure to always replace covers immediately after performing an inspection or maintenance service.
A key reason for installing these covers is a dust and contaminant shield. Any airborne debris that may enter your machine can contaminate the spindle motor and other spindle parts. This typically results in excess vibration, unnecessary wear and contaminated lubrication. Replacing covers isn’t a substitute for proper machine maintenance, but it can minimize the amount of internal cleaning and lubrication replacement.
6. Monitor and Maintain Spindle Cooling Systems
Some spindles are equipped with chiller units. These systems are typically used in high-speed applications. Work with a qualified technician to monitor and maintain this system to ensure proper cooling of high-speed spindles.
7. Work With Certified Repair Technicians
At Superior Spindle, we offer certified spindle repair, replacement and rebuild services for your industry. Be sure to work with a certified team and ask about ISO documentation. This ensures quality control and a long-lasting spindle for your manufacturing process. Proper repair protocols increase the lifetime of your tooling and allow you to continue to provide cutting-edge manufacturing to your customers.
Why Superior Spindle?
Quality repairs are about more than just providing a reliable solution to your spindle failure. We understand your business. We know how critical these operations are. We support your repair needs with an open repair line 24 hours a day, 365 days a year.